Одним из популярных методов изготовления объемных изделий из цветных металлов является горячая штамповка. При данном способе обработки металлов давлением, заготовка разогревается до температуры от 200 до 1300 градусов Цельсия, после чего подвергается деформации при помощи открытого или закрытого штампа.
Какие еще существуют особенности данной процедуры и какими преимуществами, по сравнению с другими методами обработки металлов, она обладает — об этом мы расскажем в данной статье.
Особенности техпроцесса горячей объемной штамповки
Горячая объемная штамповка, а точнее, ее технологический процесс, имеет ряд особенностей и разрабатывается согласно следующим рекомендациям:
- выбор метода изготовления — в штампе с открытым или закрытым ручьем;
- разработка детального чертежа штампованного изделия;
- определение точного количества переходов, которые необходимо выполнить для придания заготовке необходимой формы;
- разработка отдельного чертежа для каждого из переходов;
- выбор оборудования и формы для каждого из этапов техпроцесса;
- выбор способа и режима нагрева заготовки;
- определить перечень финишных операций, благодаря которым штампованная заготовка превратится в готовое изделие.
Как видите, несмотря на кажущуюся простоту, горячая штамповка — это весьма сложный технологический процесс, который требует грамотного подхода к его реализации. Однако наряду с этим, такой метод обработки металлов давлением обладает некоторыми преимуществами, о которых мы расскажем в следующем блоке нашего материала.
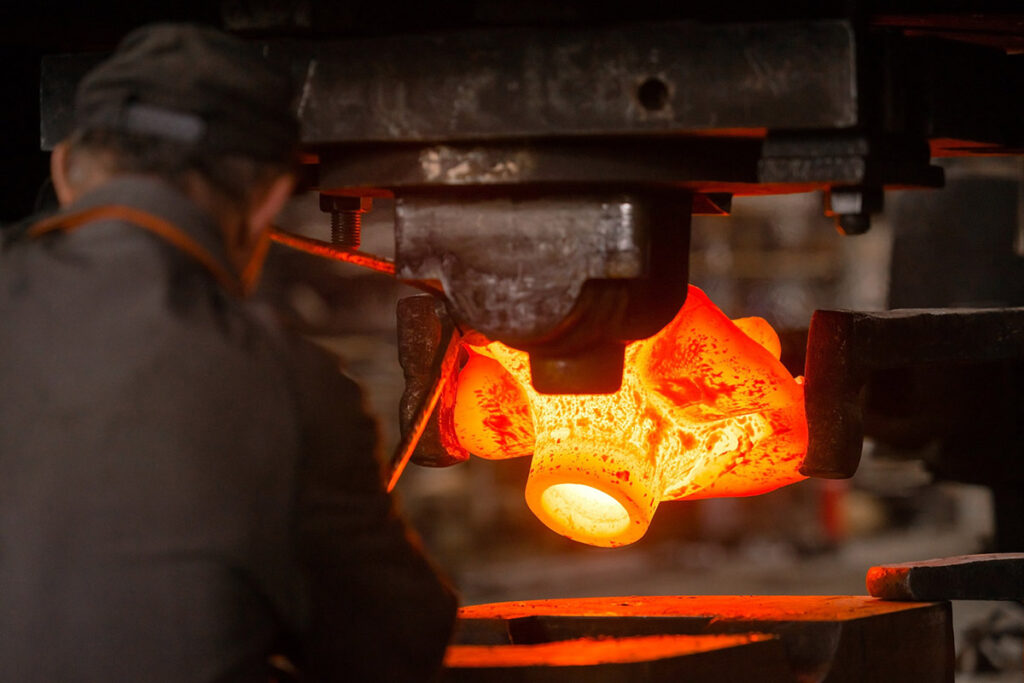
Преимущества горячей объемной штамповки
Горячая штамповка латуни и других цветных металлов обладает следующими преимуществами:
- Возможность получения заготовки, размеры которой максимально приближены к габаритам готовой детали. А это, в свою очередь, способствует снижению расхода металла при последующей механической обработке поковки и существенно облегчает процесс ее проведения.
- Однородность структуры готовых изделий, что увеличивает их прочность.
- Минимальный риск возникновения внутренних дефектов.
- Возможность изготовления большого количества однотипных изделий в сжатые сроки.
- Относительно невысокая себестоимость готовых изделий.
Все эти преимущества по достоинству оценят владельцы мелких машиностроительных предприятий, которые, в связи с постоянным развитием данной отрасли, испытывают острую необходимость в большом количестве недорогих однотипных деталей. Поэтому если вы относитесь к данной категории лиц, звоните нам прямо сейчас и оставляйте свою заявку на услугу горячей штамповки металла.
Почему выбирают нас?
Горячая листовая штамповка — это одна из услуг, которые предоставляет своим клиентам ООО «ШЛЯХ». Почему выбирают нас?
- оперативное изготовление любого количества изделий по индивидуальным или типовым проектам;
- организация доставки партии готовых изделий в любую точку Украины;
- большой ассортимент продукции и услуг;
- лояльная ценовая политика;
- индивидуальный подход к каждому клиенту.
Для получения дополнительной информации или оформления заявки на горячую штамповку стали, свяжитесь с нашим менеджером любым удобным для вас способом — по телефону, электронной почте или посредством заказа обратного звонка. Наш специалист ответит на все ваши вопросы относительно интересующей вас услуги, озвучит предварительную стоимость работ, а также оперативно оформит заявку и передаст ее в работу соответствующим подразделениям нашего предприятия.
Горячая штамповка от ООО «ШЛЯХ» — это высокое качество готовых изделий по доступной стоимости.
Свяжитесь с нами
Обращайтесь за указанными телефонами и мы обязательно Вас
проконсультируем. Всегда рады помочь!